Inspection and Maintenance Regimes for Tool Tether Systems
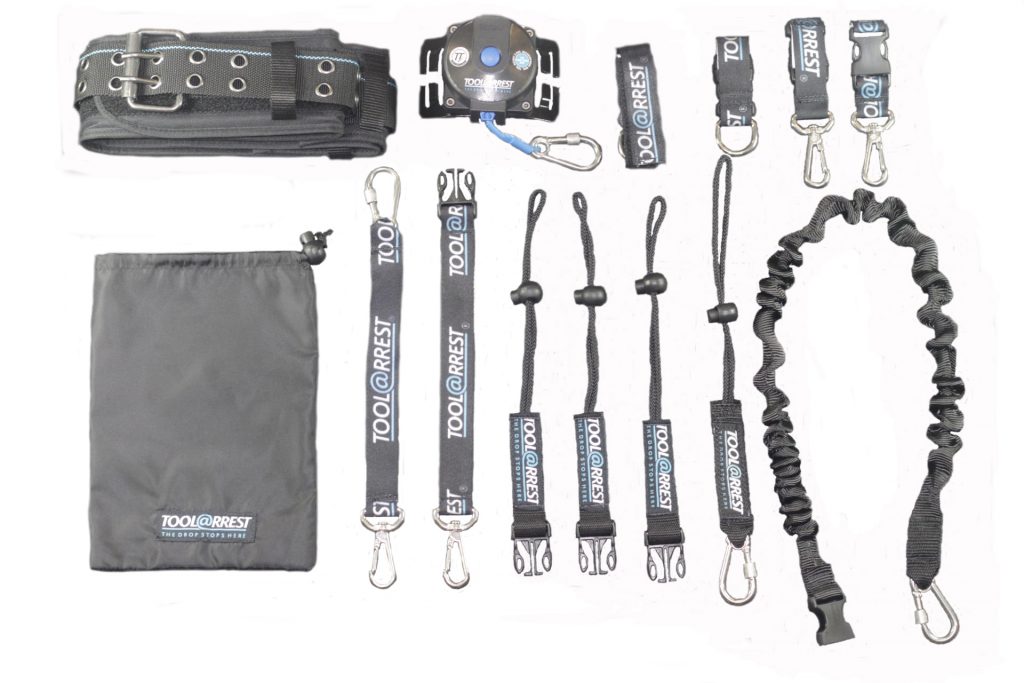
Our tool tether systems are rigorously tested to ensure they are up to the job. However, they only maintain their safety credentials if they are free from damage, wear and tear. It is vital that all tool tethering solutions are inspected and maintained regularly to keep them in good working order and protect your team and premises.
Why is Inspection and Maintenance of tool tether systems so Important?
When designing our tool tethers and anchors, we ensure that the system is suited for purpose and is capable of performing under a drop situation up to the maximum load. After comprehensive testing, each solution is then certified for its maximum load rating.
Unfortunately, damage to tethering equipment can weaken its structure and impact its effectiveness. If a tether is weakened because of a tear or abrasion, it may not hold up in a fall situation and could endanger people below. It’s crucial that inspection and maintenance regimes are put in place so damage can be spotted before it becomes a hazard.
What Inspections and Maintenance Regimes Do I Need?
Tool tethers should be inspected and maintained in accordance with the manufacturer’s guidance. This should include the following as a minimum:
• a pre-use visual inspection by the user on a daily basis
• an inspection by a competent person at intervals determined by the suppliers/manufacturers with appropriate records kept
• a quarantine procedure for taking tools and/or tethers out of service when a defect is identified
Remember that we are always on hand to help you define a formal, rigorous process before implementing a tethered tool programme. Please contact our specialist team for assistance.
Tool@rrest – The Drop Stops Here.