6 Tool Tethering Myths Debunked
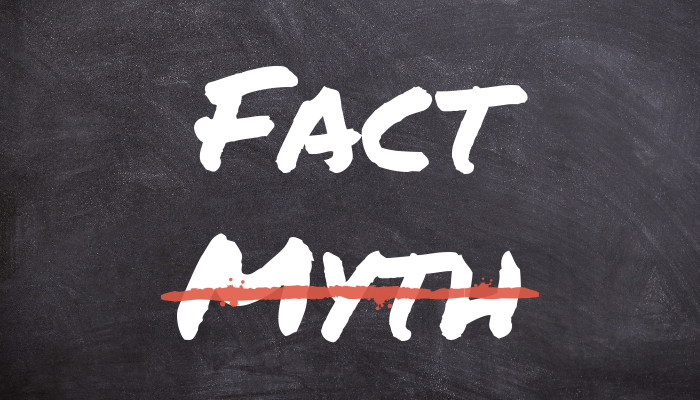
Common misconceptions about tool tethering must be tackled. If they are allowed to persist, they can stop teams from taking appropriate safety measures and could even result in an accident.
Myth 1: Tool tethering is only needed when tools are far above ground level
There isn’t a minimum level for a task to qualify as working at height. Rather, ‘working at height’ reflects the potential risk that a person could fall a distance that could result in an injury. The same principle applies to tool tethering: it is not the actual height that matters, but the risk of falling tools causing an accident. Tool tethering may even be required below ground level if teams are working above one another.
Myth 2: You can get away without tool tethering
According to the latest statistics from HSE’s Riddor Report 2017/18, dropped objects rank in the top 3 of the most deadly workplace accidents in the UK. Falling objects also accounted for over 7,000 reported non-fatal injuries, with 75% of them resulting in over 7 days of lost work time each (2016/17). Clearly, a dropped tool prevention strategy is a must if you want to keep your team safe and working well.
Myth 3: Tool tethering is the workers responsibility
While it’s true that employees must be diligent in their work to remain safe, under the Work at Height Regulations 2005, it’s the duty of employers to control any activity to keep their workforce safe. As part of the Regulations, you must ensure that risks have been properly assessed and appropriate work equipment is selected and provided to employees with adequate training. This includes tool tethering equipment when necessary. It is not the worker’s responsibly, nor would it be safe for workers to source or create their own tool tethering systems.
Myth 4: It’s OK to use homemade tethers
Sometimes, we see homemade tethers made with rope, tape or unsuitable key rings, used in an attempt to prevent dropped tools. Unfortunately, homemade tethers are themselves a major cause of incidents. Such solutions are often not reliable or certifiable and have no mechanism for traceability or inspection.
Myth 5: Tool tethering wastes time
It’s a common misconception that tool tethering can slow workers down. If tool tethering is carefully planned and carried out with well-designed equipment, this does not have to be the case. Good training will also make sure that teams can use equipment efficiently. Tool tethering systems can even save time by creating a more organised tool system and make sure that tools are always accounted for.
Myth 6: Tool tethering is too expensive
There are many options available when it comes to tool tethering. From specialist tool kits, to retrofitting your existing tools or self-tethering options. While these inevitably involve some cost, compared to the cost of an accident, tool tethering is well worth the investment. As well as injuries to team members, dropped tools can themselves be damaged or cause damage to other structures or equipment during their fall. There may also be litigation costs associated with an incident that could have been prevented.
If you’d like to discuss your tool tethering requirements, please get in touch with the Tool@rrest team or call: +44 (0) 1952 292 782.
Tool@rrest – The Drop Stops Here.